Summary:The design and construction of an ATV drive belt play a crucial role in determining its overall durability and performance. Here are some key factors to consider:
Material Composition: High-performance ATV drive belts leverage cutting-edge material t......
The design and construction of an ATV drive belt play a crucial role in determining its overall durability and performance. Here are some key factors to consider:
Material Composition: High-performance ATV drive belts leverage cutting-edge material technologies. These may include proprietary blends of aramid fibers, carbon fiber reinforcements, and specialized polymers. The careful selection of materials aims to achieve a harmonious balance between strength, heat resistance, and longevity, ensuring that the drive belt can withstand the demanding conditions of off-road use.
Cord Construction: Within the drive belt, the cords are not merely components but intricately woven elements strategically placed for maximum effectiveness. The precision in cord placement and weaving patterns involves engineering considerations to optimize tensile strength. Whether it's aramid or Kevlar fibers, these cords are integrated in a way that minimizes stretching and maximizes durability, contributing to the overall robustness of the drive belt.
Width and Thickness: The dimensions of the ATV drive belt are meticulously engineered to facilitate dynamic power transfer. This involves a deep understanding of the ATV's power requirements and the creation of a belt with specific width and thickness dimensions. The goal is to maximize the contact area with the pulleys, ensuring efficient power transmission, minimizing energy loss, and enhancing overall ATV performance.
Curing Process: The curing process in manufacturing is a scientific endeavor. It involves precise control over factors such as temperature, pressure, and duration. Scientific vulcanization techniques ensure that the belt undergoes a controlled transformation, achieving consistent hardness and flexibility. This process is critical for producing a drive belt with uniform properties, capable of maintaining its structural integrity under diverse and challenging operating conditions.
Tooth Profile: Toothed drive belts undergo microscopic engineering of their tooth profile. This involves intricate design considerations to optimize the shape, size, and spacing of the teeth. The microscopic precision ensures secure engagement with the pulleys, reducing any possibility of slippage. This meticulous tooth engineering is essential for efficient power transfer, especially in situations where the ATV encounters uneven terrain or varying loads.
Heat Dissipation: The heat dissipation capabilities of modern ATV drive belts go beyond basic principles. Innovative cooling architectures may include integrated cooling channels or the use of materials with enhanced thermal conductivity. These features are designed to efficiently dissipate heat generated during operation. By preventing overheating, the drive belt remains within optimal temperature ranges, reducing wear and tear and ensuring sustained performance over extended periods.
Flexibility: Achieving the right balance between flexibility and stiffness involves nanostructural engineering. Materials are chosen and processed at a microscopic level to impart strategic flexibility while maintaining the necessary stiffness. This level of engineering precision ensures that the drive belt adapts seamlessly to the dynamic movements of the ATV, conforming to pulley contours with precision. The result is a drive belt that remains supple under various conditions, preventing undue stress and maintaining consistent tension.
Resistance to Contaminants: The resistance to contaminants is not a superficial feature but a result of nano-coating technologies and sealed integration. Nano-coatings protect individual components at a microscopic level, preventing the intrusion of contaminants. Sealed integration involves the incorporation of protective layers and seals throughout the belt's structure, creating a robust barrier against mud, water, and debris. This multi-layered defense ensures that the drive belt remains resilient, even when subjected to the harshest off-road conditions.
Scooter Belt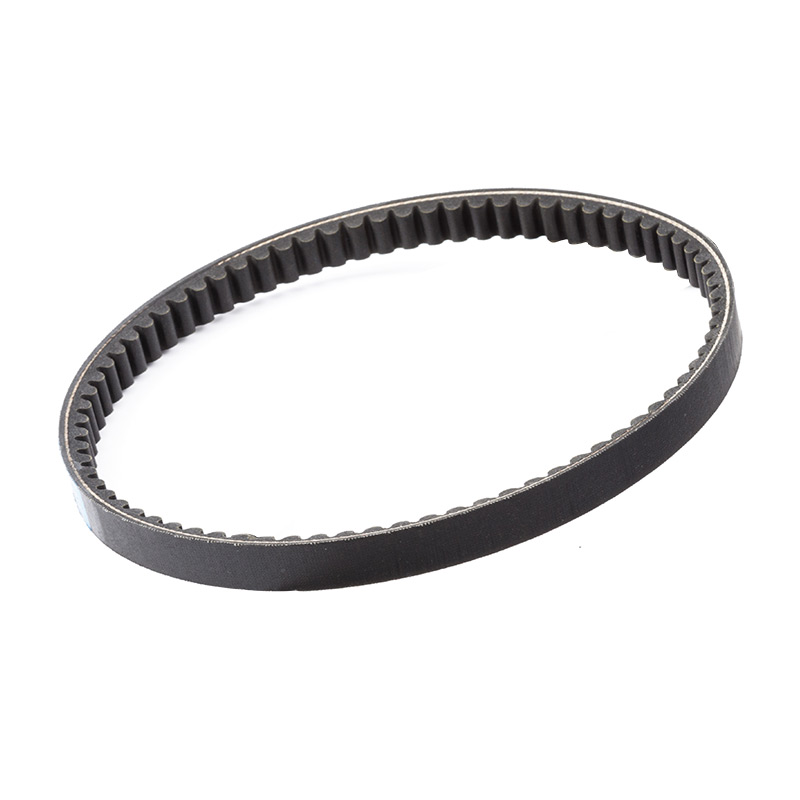